Saturday, June 12, 2010
Purchasing Value Keys
In the material master record, you can store rules governing the admissibility of over- and under-deliveries through Purchasing Value Keys.
Various keys can be defined for different values:
Delivery tolerance limits
Percentage (based on the order quantity) up to which an under-delivery/over-delivery of this item will be accepted or if unlimited over-delivery is acceptable. 5 percentage has been defined for the key 2 here:
No configuration changes made here for Tatra.
Labels:
Configure Purchasing value Keys,
MM,
SAP,
SAP MM
Defining Material Groups
In this IMG activity, you define material groups to group together materials with the same attributes or purpose.
You can use material groups to:
• Limit the scope of analyses
• Systematically search for material master records via matchcodes
At the IMG menu as shown define the material groups.
Maintain entries as below:
You can use material groups to:
• Limit the scope of analyses
• Systematically search for material master records via matchcodes
At the IMG menu as shown define the material groups.
Maintain entries as below:
Labels:
Define Material Group,
Material Group,
MM,
SAP,
SAP MM
Field Selection
In this section, you Define whether a field is hidden or displayed, or whether an entry is mandatory or optional in material master maintenance by assigning the field to a field selection group.
Field selection group:
Group of several fields to which the same field option applies. The field options are as follows:
• Hide
• Display
• Required entry
• Optional entry
Each field selection group has a number between 1 and 240. User defined groups are numbered from 210 onwards.
Assign Fields to Field Selection Groups:
To define whether a field is hidden or displayed, or whether an entry is mandatory or optional in material master maintenance, you must assign the field to a field selection group. You may assign a field to one field selection group only.
For example the field Purchasing Group is to be mandatory. The field is MARC-EKGRP. The field selection group is 214. This group controls the field EKGRP and the case when it is to be made mandatory/ optional for entry etc.
The field reference ROH is the field reference as maintained in the attributes of Material Type ROH. By selecting the option “Reqd Entry” for these Field References, the fields are made mandatory for all materials of type which have the reference as ROH.
Labels:
field Selection,
Material Master Field Selection,
MM,
SAP,
SAP MM
Define Number Ranges for Each Material Type
In this step, you define the type of number assignment and the number range intervals for material master records. When creating a material master record, you must assign it a unique number. There are two ways of doing this:
- internal number assignment
In this case, a number within the number range interval allowed is assigned by the SAP R/3 System.
- external number assignment
Here, the user assigns a number within the number range interval allowed. You can define the intervals for external number assignment numerically and alphanumerically.
TATRA uses external number ranges.
Define Attributes of Material Types
Whenever you create a material master record, you must assign it to a material type. This requires you to first define the attributes of each material type. You do this in this IMG activity.
The following options are available here:
• Customizing the existing material types in the R/3 System if necessary
You do this by selecting the material type and choosing Details.
• Creating new material types
You do this by copying an existing material type. In each case, define the attributes of each material type as required.
For each material type, you can allow movements in quantity to be updated in all valuation areas, in some valuation areas, or in none. Likewise, you can allow value flows to be updated in all valuation areas, in some valuation areas, or in none.
Choose the material type for which the attributes are to be defined:
The attributes of the material type are defined in the following screen. The significance of the fields are detailed later.
Field reference for material master
When material master records are maintained, the field reference determines for each field selection group if the field selection group is set to Hide, Display, Required entry, or Optional entry. See the section “Field Selection” for configurations related to this.
Default value for material item category group
The system determines the item category on the basis of the item category group, to which the material is assigned, and the transaction-specific data, that is defined in a table. It then proposes this item category in the document concerned. In the material master this value is defaulted for the materials of this type.
Screen reference depending on the material type
Grouping of material types that determines what screens are displayed depending on the material type when you maintain material master records. It also determines the order in which the screens appear.
Material Is Costed with Quantity Structure
This indicator determines whether the material is costed using costing with or without a quantity structure.
Manufacturer Part
Identifies materials of this material type as manufacturer parts.
Price Control Indicator
Indicates the price control used to valuate the stock of a material. You have the following options:
Standard price
Moving average price
External purchase orders allowed
Allows external purchase orders, that is, external procurement of the material – option 2.
Account category reference
Group of valuation classes that the system uses to check whether the valuation class you have entered is allowed when you maintain accounting data in a material master record. All the permitted valuation classes for the material type are assigned thru this Account Category Reference.
Price Control Mandatory
Determines whether the price control indicator defined for the material type appears as a default value (indicator not set) or a fixed value (indicator set) when material master records are created or changed.
Update Movements in Quantity /Value Flows in All Valuation Areas
Defines whether movements in quantity are updated identically in all/some/no existing valuation areas.
If it is for some valuation areas, by double-clicking Quantity/value updating, you can select or deselect the valuation areas in which value flows are to be updated. If value flows are not updated identically in all valuation areas, the By valuation area indicator is set automatically.
User DepartmentsSelect which views are to be made to appear while maintaining material master data for this material type.
Labels:
define attributes of Material type,
Material type,
MM,
SAP,
SAP MM
Configuring the Material Master:
In this section, you can configure the material master to suit your specific needs. You can do the following:
1. Define the structure of the data screens. A data screen is a display in the material master such as:
• View, that is, main screen such as Basic Data that you can select in the Select View(s) dialog box
• Secondary screen, of which there are the following types:
o Additional screen such as Descriptions that you can access from every view
o Screen that you can access in a view, for example, Production Versions from the MRP view in the standard material master.
2. A data screen is made up of individual subscreens. You can, for example, remove subscreens that you do not require from a particular data screen, include others from other data screens, or include subscreens of your own.
• Group screens together to form a screen sequence
Define Structure of Data Screens for Each Screen Sequence:
In this IMG activity, you have the following navigation levels:
• Screen sequences
This overview appears when you access the IMG activity. It contains all existing screen sequences. You have the following options:
o Creating screen sequences by copying existing screen sequences
You can create a new screen sequence by selecting an existing screen sequence and choosing Copy as. You are required to enter a new screen sequence ID and description, and to choose Enter. The system copies the screen sequence selected, the data screens, the subscreen assignments, and the order of the data screens.
o Deleting screen sequences
You can delete screen sequence(s) by selecting them as required and choosing Delete. The system deletes the screen sequence selected, the relevant data screens, and the subscreen assignments (not the subscreens themselves).
o Transporting screen sequences and data screens
You can transport screen sequences and/or data screens from the test system to the production system by selecting the screen sequence(s) and/or data screen(s) required and transporting them in the usual way.
The screen sequence Z1 for TATRA has been created as a copy of standard sequence 99.
To view the data screens available for the screen sequence Z1, select the option “Data Screens”.
To see the sub-screens that are present within a screen, select the screen, say screen 15, and select the “Subscreens” option.
The list of subscreens that are available within this screen are seen here. By selecting the subscreen and using the option button “View Subscreen”, you can view the fields in the subscreen.
In the above case when the option “View Subscreen” is chosen the following subscreen is shown.
Assign Screen Sequences to User/Material Type/Transaction/In:
In this IMG activity, you can assign a screen sequence to a combination of one or more transactions, users, material types, or industry sectors.
Refer the screen sequence Z1 for all the Screen Reference Groups as below:
Authorization for Vendor Master CIN tab
For the users who are to be given authorization for CIN data tab in the vendor master, use the option “User Screen Reference” on the following screen.
In this section, you can configure the material master to suit your specific needs. You can do the following:
1. Define the structure of the data screens. A data screen is a display in the material master such as:
• View, that is, main screen such as Basic Data that you can select in the Select View(s) dialog box
• Secondary screen, of which there are the following types:
o Additional screen such as Descriptions that you can access from every view
o Screen that you can access in a view, for example, Production Versions from the MRP view in the standard material master.
2. A data screen is made up of individual subscreens. You can, for example, remove subscreens that you do not require from a particular data screen, include others from other data screens, or include subscreens of your own.
• Group screens together to form a screen sequence
Define Structure of Data Screens for Each Screen Sequence:
In this IMG activity, you have the following navigation levels:
• Screen sequences
This overview appears when you access the IMG activity. It contains all existing screen sequences. You have the following options:
o Creating screen sequences by copying existing screen sequences
You can create a new screen sequence by selecting an existing screen sequence and choosing Copy as. You are required to enter a new screen sequence ID and description, and to choose Enter. The system copies the screen sequence selected, the data screens, the subscreen assignments, and the order of the data screens.
o Deleting screen sequences
You can delete screen sequence(s) by selecting them as required and choosing Delete. The system deletes the screen sequence selected, the relevant data screens, and the subscreen assignments (not the subscreens themselves).
o Transporting screen sequences and data screens
You can transport screen sequences and/or data screens from the test system to the production system by selecting the screen sequence(s) and/or data screen(s) required and transporting them in the usual way.
The screen sequence Z1 for TATRA has been created as a copy of standard sequence 99.
To view the data screens available for the screen sequence Z1, select the option “Data Screens”.
To see the sub-screens that are present within a screen, select the screen, say screen 15, and select the “Subscreens” option.
The list of subscreens that are available within this screen are seen here. By selecting the subscreen and using the option button “View Subscreen”, you can view the fields in the subscreen.
In the above case when the option “View Subscreen” is chosen the following subscreen is shown.
Assign Screen Sequences to User/Material Type/Transaction/In:
In this IMG activity, you can assign a screen sequence to a combination of one or more transactions, users, material types, or industry sectors.
Refer the screen sequence Z1 for all the Screen Reference Groups as below:
Authorization for Vendor Master CIN tab
For the users who are to be given authorization for CIN data tab in the vendor master, use the option “User Screen Reference” on the following screen.
Labels:
Configuring Material type,
Material type,
MM,
SAP,
SAP MM
MM Enterprise Structure Configuration
MM Enterprise Structure Configuration
Settings at Enterprise Structure - Definition
Define valuation level:
You define the valuation level by specifying the level at which material stocks are valuated. You can valuate material stocks at the following levels:
• Plant level
Valuation must be at this level if you want to use the application component Production Planning (PP) or Costing
• Company code level
The decision you make is valid for the whole client. SAP recommends setting material valuation at plant level. Once set, it is not possible to switch the valuation level from plant to company code, or vice versa.
Choice of valuation level affects the following among others:
• Maintenance of material master records
Depending on the valuation level chosen, accounting data (in particular the valuation price) is maintained for each plant or for each company code in the material master record.
At the IMG Menu, select the option shown:
The system by default sets the valuation at Plant Level.
Define Plant:
The plant is an operating area or branch within a company.
The plant is embedded in the organizational structure as follows:
• The plant is assigned to a single company code. A company code can have several plants.
• Several storage locations in which material stocks are managed can belong to a plant.
• A single business area is assigned to a plant and to a division.
• A plant can be assigned to several combinations of sales organization and distribution channel.
• A plant can have several shipping points. A shipping point can be assigned to several plants.
• A plant can be defined as a maintenance planning plant.
A plant has the following attributes:
• A plant has an address.
• A plant has a language.
• A plant belongs to a country.
• A plant has its own material master data. You can maintain data at plant level for the following views on a material master record in particular: MRP, Purchasing, Storage, Work scheduling, Production resources/tools, Forecasting, Quality management, Sales, Costing.
The plant plays an important role in the following areas:
• Material valuation : If the valuation level is the plant, the material stocks are valuated at plant level. If the valuation level is the plant, you can define the material prices for each plant. Each plant can have its own account determination.
• Inventory management : The material stocks are managed within a plant.
• MRP : Material requirements are planned for each plant. Each plant has its own MRP data. Analyses for materials planning can be made across plants.
• Production
• Costing : In costing, valuation prices are defined only within a plant.
• Plant maintenance : If a plant performs plant maintenance planning tasks, it is defined as a maintenance planning plant. A maintenance planning plant can also carry out planning tasks for other plants (maintenance plants).
At the IMG Menu choose option as below:
Use the New Entries Option to create a new plant. Choose the “Details” option to add address, language, calendar and other details.
Maintain the address details in the address tab:
Choosing the Address option opens the dialog box as seen in screen below:
Maintain the details in the dialog box. In the main screen maintain the factory Calendar.
Jurisdiction Code must be Blank as we are using TAXINN.
Maintain Storage Locations
A storage location is the place where stock is physically kept within a plant.
A storage location has the following attributes:
• There may be one or more storage locations within a plant.
• A storage location has a description and at least one address.
• It is possible to store material data specific to a storage location.
• Stocks are managed only on a quantity basis and not on a value basis at storage location level.
• Physical inventories are carried out at storage location level.
• Storage locations are always created for a plant.
At the IMG Menu as in screen below, choose “Maintain Storage Location”.
In the screen below choose the plant for which Storage Locations are to maintained:
Maintain the Storage Location name and description in the new entries screen.
Maintain Purchasing Organization:
In this step, you set up your purchasing organizations.
From the Materials Management and Purchasing view, the purchasing organization is responsible for all purchasing activities (including the processing of requests for quotations and purchase orders, for example).
The purchasing organization is integrated within the organizational structure as follows:
• A purchasing organization can be assigned to several company codes.
(= Corporate-group-wide purchasing).
• A purchasing organization can be assigned to one company code.
(= Company-specific purchasing).
• A purchasing organization can also exist without being assigned to a company code.
o Since each plant must be assigned to a company code, the latter can be determined via the plant at the time of each procurement transaction even if the procuring purchasing organization has not been assigned to a company code.
• A purchasing organization must be assigned to one or more plants.
(= Plant-specific purchasing).
• A purchasing organization can be divided into several purchasing groups that are responsible for different operational areas.
• Each purchasing organization has its own info records and conditions for pricing.
• Each purchasing organization has its own vendor master data.
• Each purchasing organization evaluates its own vendors using MM Vendor Evaluation.
• Authorizations for processing purchasing transactions can be assigned to each purchasing organization.
• All items of an external purchasing document, that is, request for quotation, purchase order, contract, or scheduling agreement, belong to a purchasing organization.
• The purchasing organization is the highest level of aggregation (after the organizational unit "client") for purchasing statistics.
• The purchasing organization serves as the selection criterion for lists of all purchasing documents.
For TATRA the following are defined:
Cross Plants Purchasing Organisation
A purchasing organization is responsible for the purchasing activities many plants. In this case you attach the purchasing organization to many plants. For Tatra two purchasing oragnisations are defined :
1000 :For regular purchase
1001 :For capital items.
Each of these plants can be responsible for purchasing activities in any other plant :
Choose the IMG menu as in screen below:
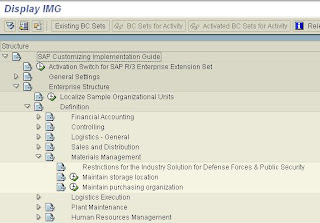
Maintain the name and description of the Purchasing Organization in New Entries.
Assignments of Enterprise Structure Elements
Assign plant to company code
A plant can only belong to one company code.
The assignments maintained are below:
Assign Purchasing Organization to Company Code & Plant:
In this Implementation Guide (IMG) activity, you assign purchasing organizations to company codes and also to plants.
Purchasing Organization and Plants :
----------------------------------------------------------------------------------------------------------------
Labels:
Configuration,
Enterprise,
MM,
SAP,
SAP MM,
structure
Subscribe to:
Posts (Atom)